I wasn’t going to post about this problem, but I guess I can take the expected ragging and although I am fairly certain I already know what I should do, the fact is I’m not sure, so maybe this is worth posting.
About 2 years ago I rebuilt my FE (broke a piston; timing set wrong as balancer had slipped) and as I was torquing the rod nuts, I came across one that felt funny. It did come up to torque, but seemed to come up more slowly than all the rest. In other words, it took more of a turn to get that last bit of full torque.
For example, if all the other rod bolts took ¼ turn to got from 40 ft-lbs to the last step of 50 ft-lbs, the one bolt in question took more like ½ turn.
I gave it a good visual inspection, removed the bearing shells to check for grit behind them, tried swapping nuts, but couldn’t find anything wrong. (I didn’t really know much about measuring bolt stretch at that time).
Based on the fact these were ARP rod bolts, only torqued 5 or 6 times, and had 4000 miles on the engine, I decided to continue on with the assembly. Also, when applying torque, it didn’t feel like the bolt was stripping, as the torque did keep building. When threaded fasteners strip, the torque flattens out, and then drops as the threads become more an more damaged. My experience with stretching bolts is limited to removal of rusty stuff, and in those cases, the bolt doesn’t seem to yield at all, but suddenly snaps off. But that’s more of a shear thing than tension.
So, mistake number one; I finished the engine assembly without ever finding out what was going on as well as rectifying the problem. Yes I feel stupid about that now.
Eventually I removed the oil pan (for a variety of reasons) and checked the rod in question. Everything looked fine, and the nuts didn’t move with the torque wrench set to spec. This was after about 1000 miles of operation. I might have hit 6000 rpm a few times, but generally I short shift just having fun on the street.
Mistake number 2: I buttoned it up again without finding out and fixing what might have been wrong. Admitting that makes me feel twice as stupid.
I’ve now driven another 500 trouble free miles and everything is working fine. But I have this nagging thought the bolt might fail.
As I’m still worried, I’m thinking of replacing the bolt, however in the meantime, I did a bit of research and also some rod bolt testing.
I thought I’d share what I found out as it may prove of interest to all of you, but take it with a grain of salt. My measuring technique was without a proper stretch gauge, and I'm not sure if I understand all the theory 100%.
1/ I tested a couple of old (stock) connecting rods had from a 390 parts engine. Interestingly, one of the 4 rod bolts I tightened, felt the same as the mystery bolt in my engine. Basically, the torque came up more smoothly and slowly than the other 3.
This could be explained by the following pie-chart which shows how much of the applied torque is wasted in frictional forces. Basically, if the nut seat on the connecting rod cap and/or the bolt threads were a bit more burnished than the other bolts/caps, this could explain it. A bolt failure analysis I found on the net had this to say:
i. The thread friction coefficient could vary between 0.14 and 0.25.
ii. The under-head friction coefficient could vary between 0.10 and 0.18.
That’s a lot of change from one seemingly identical fastener to another.
![]()
2/ Next I decided to try to measure the stretch. It wasn’t easy as I only had digital callipers to work with and these Ford Factory bolts have uneven ends. Here’s what I found out about stretch:
At 40 ft-lbs, there was no stretch that I could detect.
At 50 ft-lbs, the stretch was about 0.004
At 60 ft-lbs, the stretch was about 0.009
Keep in mind, these Ford bolts have a torque spec of 45 ft-lbs and my ARP bolts in the engine have a 50 ft-lb spec.
3/ For the next step I decided to torque to yield. Basically, the torque tapered off around 70 ft-lbs and then dropped to 65 ft-lbs. It stayed at 65 ft-lbs for many turns of the wrench as the bolt stretched. I never did go much further to see if it would break. See below:
![]()
ARP states their specs are for a 75% clamp load. You can see that’s quite a ways down from the yield point and on the linear portion of the stress-strain curve.
![]()
It appears that when my test bolt stretched it was high up in the yield area, and although it was really stretching, it had not yet fallen off the chart to the point of failure. The test bolt is definitely strong for its size and certainly not brittle.
When I’ve broken (other type) bolts in the past (from loosening), they have just suddenly snapped off. This was due to either corrosion on the threads or under the bolt head. My over-tightening experience has only shown up in stripped threads due to multiple disassembly and reassembly, but these wern't rod bolts either. These rod bolts really stretch, and even the one I stretched a lot, still had some spring back, although no where near its original length.
4/ Based on information from those engine-heads with more experience under their belts than I, tightening an ARP bolt by the stretch spec requires a much higher torque than the torque spec. Some thought is the type of lube used on the bolt threads and under the bolt head must be of a certain type, or the readings wont correlate.
5/ If my ARP bolt was really stretching when I tightened it, I would have either had to be above the yield point, about 67 ft-lbs (if the ARP spec of 50 ft-lbs is 75% of yield), which it wasn’t, or I would be on the downward side of the stress-strain curve and the bolt would have shown signs of stretching, which a visual inspection did not show.
6/ Based on all this, as well as the fact I’ve quite a lot of miles since the re-build, I doubt my installed ARP bolt will fail, although I may be merely trying to convince myself. Whatever I decide to do, I think I’m in the market for a proper stretch gauge.
So my questions are:
1/ Do you think the rod bolt was stretching? Other thoughts might be excessive bearing crush, deformed rod cap or nicked/burred bolt threads.
2/ Based on merely a feeling something wasn’t right, should I bite the bullet, stop running the engine, and start a teardown, or based on the engine lasting 1500 miles so far, and a check at 1000 miles indicating things are fine, just keep driving it?
3/ Has anyone ever had a similar experience tightening rod bolts, particularly ARP, and if so, what did you find out?
About 2 years ago I rebuilt my FE (broke a piston; timing set wrong as balancer had slipped) and as I was torquing the rod nuts, I came across one that felt funny. It did come up to torque, but seemed to come up more slowly than all the rest. In other words, it took more of a turn to get that last bit of full torque.
For example, if all the other rod bolts took ¼ turn to got from 40 ft-lbs to the last step of 50 ft-lbs, the one bolt in question took more like ½ turn.
I gave it a good visual inspection, removed the bearing shells to check for grit behind them, tried swapping nuts, but couldn’t find anything wrong. (I didn’t really know much about measuring bolt stretch at that time).
Based on the fact these were ARP rod bolts, only torqued 5 or 6 times, and had 4000 miles on the engine, I decided to continue on with the assembly. Also, when applying torque, it didn’t feel like the bolt was stripping, as the torque did keep building. When threaded fasteners strip, the torque flattens out, and then drops as the threads become more an more damaged. My experience with stretching bolts is limited to removal of rusty stuff, and in those cases, the bolt doesn’t seem to yield at all, but suddenly snaps off. But that’s more of a shear thing than tension.
So, mistake number one; I finished the engine assembly without ever finding out what was going on as well as rectifying the problem. Yes I feel stupid about that now.
Eventually I removed the oil pan (for a variety of reasons) and checked the rod in question. Everything looked fine, and the nuts didn’t move with the torque wrench set to spec. This was after about 1000 miles of operation. I might have hit 6000 rpm a few times, but generally I short shift just having fun on the street.
Mistake number 2: I buttoned it up again without finding out and fixing what might have been wrong. Admitting that makes me feel twice as stupid.
I’ve now driven another 500 trouble free miles and everything is working fine. But I have this nagging thought the bolt might fail.
As I’m still worried, I’m thinking of replacing the bolt, however in the meantime, I did a bit of research and also some rod bolt testing.
I thought I’d share what I found out as it may prove of interest to all of you, but take it with a grain of salt. My measuring technique was without a proper stretch gauge, and I'm not sure if I understand all the theory 100%.
1/ I tested a couple of old (stock) connecting rods had from a 390 parts engine. Interestingly, one of the 4 rod bolts I tightened, felt the same as the mystery bolt in my engine. Basically, the torque came up more smoothly and slowly than the other 3.
This could be explained by the following pie-chart which shows how much of the applied torque is wasted in frictional forces. Basically, if the nut seat on the connecting rod cap and/or the bolt threads were a bit more burnished than the other bolts/caps, this could explain it. A bolt failure analysis I found on the net had this to say:
i. The thread friction coefficient could vary between 0.14 and 0.25.
ii. The under-head friction coefficient could vary between 0.10 and 0.18.
That’s a lot of change from one seemingly identical fastener to another.
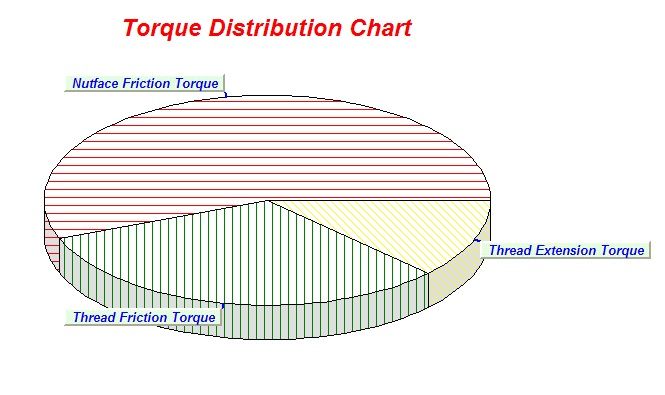
2/ Next I decided to try to measure the stretch. It wasn’t easy as I only had digital callipers to work with and these Ford Factory bolts have uneven ends. Here’s what I found out about stretch:
At 40 ft-lbs, there was no stretch that I could detect.
At 50 ft-lbs, the stretch was about 0.004
At 60 ft-lbs, the stretch was about 0.009
Keep in mind, these Ford bolts have a torque spec of 45 ft-lbs and my ARP bolts in the engine have a 50 ft-lb spec.
3/ For the next step I decided to torque to yield. Basically, the torque tapered off around 70 ft-lbs and then dropped to 65 ft-lbs. It stayed at 65 ft-lbs for many turns of the wrench as the bolt stretched. I never did go much further to see if it would break. See below:
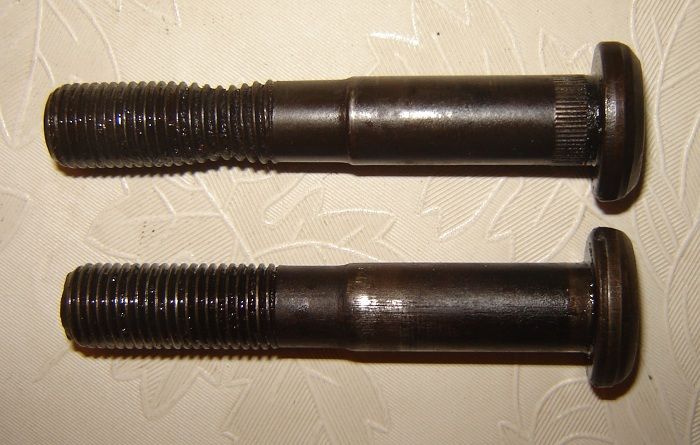
ARP states their specs are for a 75% clamp load. You can see that’s quite a ways down from the yield point and on the linear portion of the stress-strain curve.
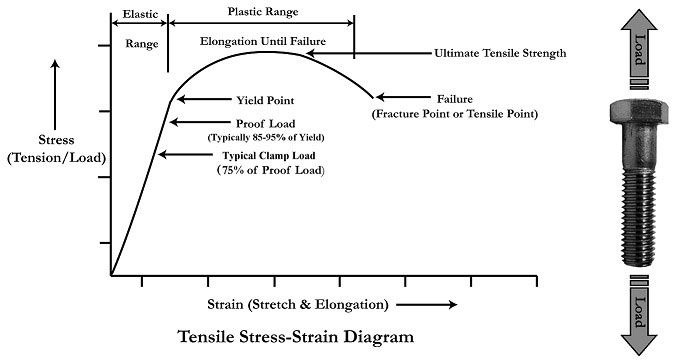
It appears that when my test bolt stretched it was high up in the yield area, and although it was really stretching, it had not yet fallen off the chart to the point of failure. The test bolt is definitely strong for its size and certainly not brittle.
When I’ve broken (other type) bolts in the past (from loosening), they have just suddenly snapped off. This was due to either corrosion on the threads or under the bolt head. My over-tightening experience has only shown up in stripped threads due to multiple disassembly and reassembly, but these wern't rod bolts either. These rod bolts really stretch, and even the one I stretched a lot, still had some spring back, although no where near its original length.
4/ Based on information from those engine-heads with more experience under their belts than I, tightening an ARP bolt by the stretch spec requires a much higher torque than the torque spec. Some thought is the type of lube used on the bolt threads and under the bolt head must be of a certain type, or the readings wont correlate.
5/ If my ARP bolt was really stretching when I tightened it, I would have either had to be above the yield point, about 67 ft-lbs (if the ARP spec of 50 ft-lbs is 75% of yield), which it wasn’t, or I would be on the downward side of the stress-strain curve and the bolt would have shown signs of stretching, which a visual inspection did not show.
6/ Based on all this, as well as the fact I’ve quite a lot of miles since the re-build, I doubt my installed ARP bolt will fail, although I may be merely trying to convince myself. Whatever I decide to do, I think I’m in the market for a proper stretch gauge.
So my questions are:
1/ Do you think the rod bolt was stretching? Other thoughts might be excessive bearing crush, deformed rod cap or nicked/burred bolt threads.
2/ Based on merely a feeling something wasn’t right, should I bite the bullet, stop running the engine, and start a teardown, or based on the engine lasting 1500 miles so far, and a check at 1000 miles indicating things are fine, just keep driving it?
3/ Has anyone ever had a similar experience tightening rod bolts, particularly ARP, and if so, what did you find out?